Check Sheet is also called as Tally Sheet and is used for collecting and analyzing data.
Data collection is an important activity in the problem solving process as it provides a basic for further action. A data may be numerical, observations and opinion.
This is the basic and very important tool of 7 QC Tools and is extensively used in Problem Solving Techniques such as 8D, PDCA and measure phase of Six Sigma.
Table of Contents
WHEN TO USE CHECK SHEET
For collecting real-time data from production processes. For example, Production data recording check sheet – part wise, model wise, machine wise and operator wise.
To distinguish between fact & opinion.
To collect data about the type of problem/defects/rejection or non-conformance.
When the data collection required from different machines, parts, models, shifts, persons and locations etc.
When to record product and process related parameters against defined work standards to ensure quality.
BENEFITS OF CHECK SHEET
Helps to analyze the data for corrective and preventive actions.
Helps in making the Bar graph, Histogram and Pareto Chart.
Helps to take decision at a glace to control the product and process related non conformance.
Helps to detect how often a problem occurs.
It facilitates systematic record keeping or data collection.
EXAMPLES
Date wise and defect wise rejection monitoring check sheet.
An example given below, shows at a glance that the major rejection contributing defects are Blow hole and crack and high rejection is on dated 1 and 2.
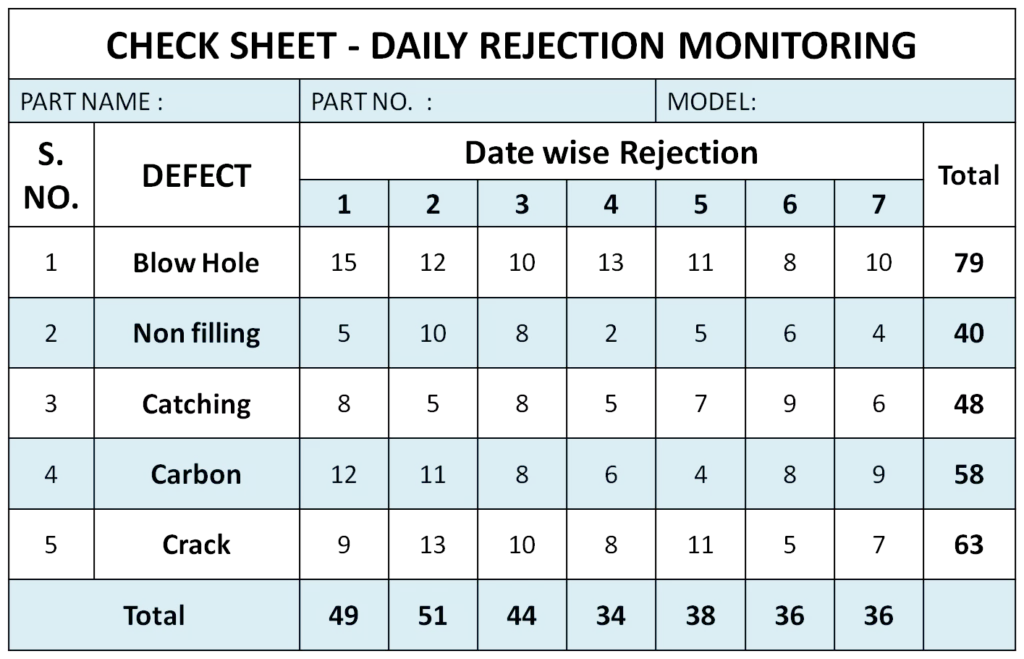
Computer related problem check sheet that shows the weekly status of problems.
An example given below, shows at a glance that the major problem are related to Email and Server Access and last fourth week having the maximum problem.
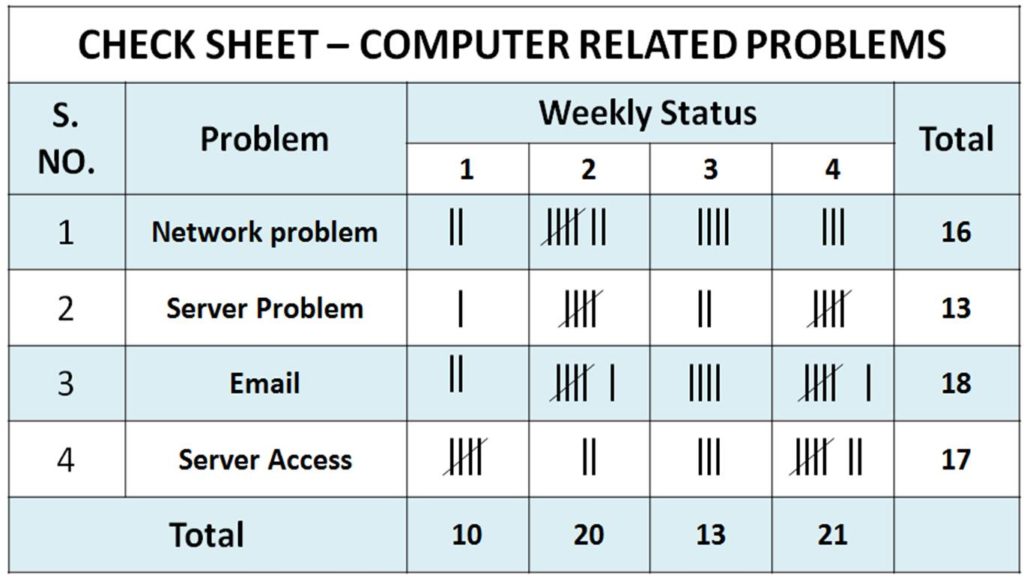
PROCEDURE TO USE
Bring clarity of understanding in the events or conditions under study.
Decide responsibility, duration and sources for Data collection.
Checksheet form is to be simple to use, easy to understand and complete in all respects for accurate data collection.