Obtaining ISO 9001:2015 Quality Management System certification involves several steps, each designed to ensure your organization’s Quality Management System (QMS) meets the rigorous standards set by ISO 9001. This certification demonstrates that your business consistently delivers products or services that meet customer and regulatory requirements, leading to improved efficiency, customer satisfaction, and marketability. Below is a step-by-step guide on how to obtain ISO 9001 certification.
Table of Contents
Step 1 | Understand the ISO 9001 Requirements
Before starting the certification process, it is crucial to fully understand the requirements of ISO 9001:2015 QMS standard.
Obtain a copy of the ISO 9001 standard: You can purchase the standard from official organizations like the ISO website or local standards bodies.
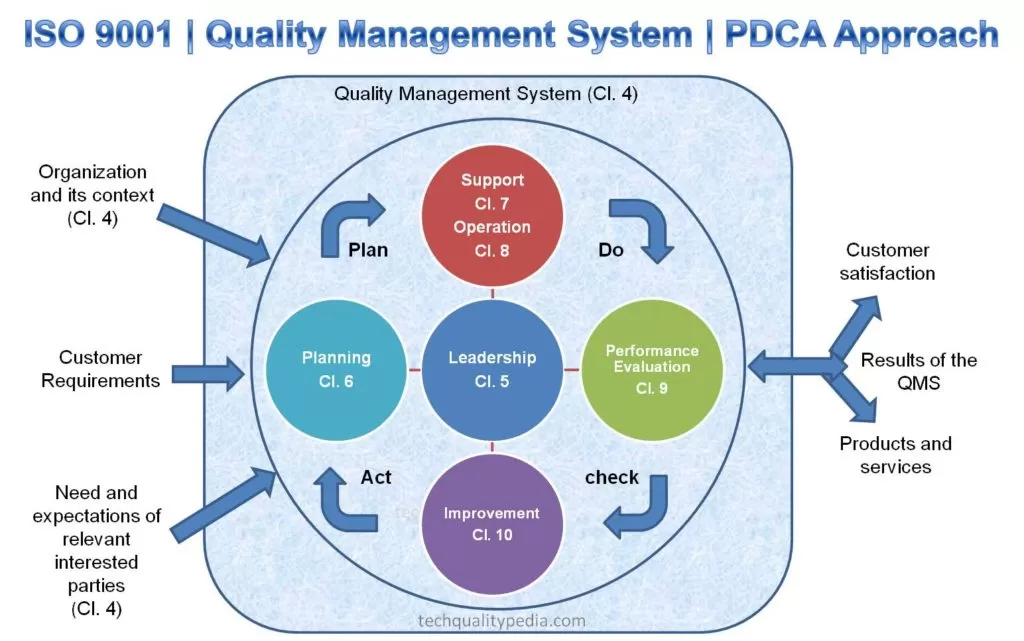
- Familiarize yourself with the ISO 9001 clauses and requirements: The latest ISO 9001:2015 standard is divided into 10 clauses that are based on the High-Level Structure-HLS, including:
- Scope
- Normative References
- Terms and Definitions
- Context of the organization
- Leadership
- Planning
- Support
- Operation
- Performance evaluation
- Improvement
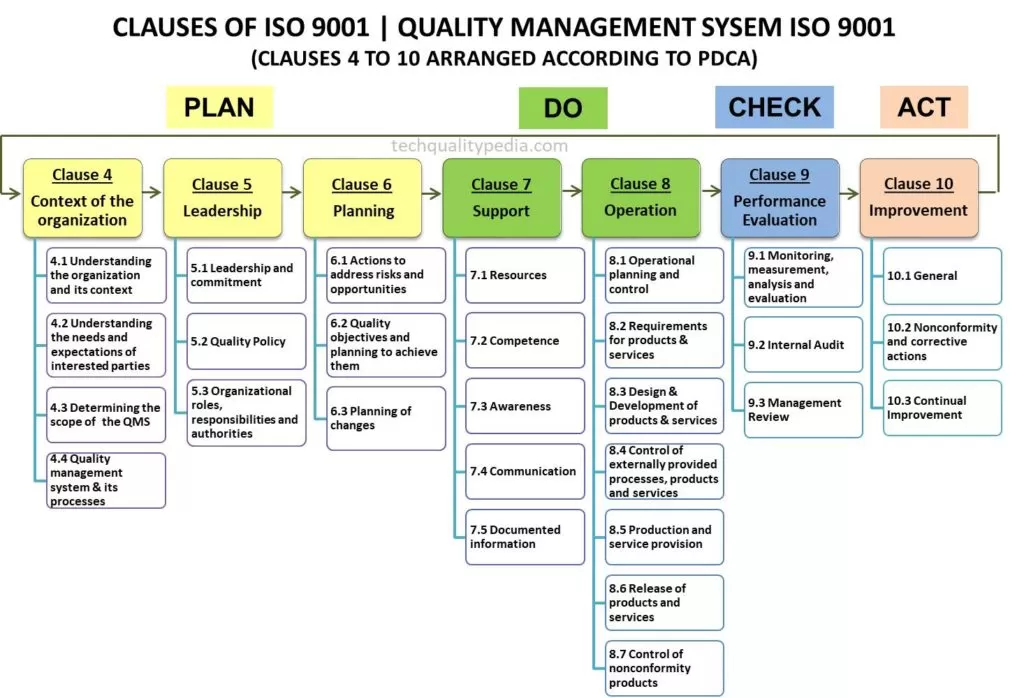
Step 2 | Perform a Gap Analysis
A proper gap analysis helps you to identify the difference between your present/current processes and the ISO 9001 requirements. It’s essentially an internal audit of your existing Quality Management System-QMS, which allowing you to identify areas for improvement.
- Internal Gap Analysis: If you have a QMS Manager, Management Representative, or Internal Qualified auditors of ISO 9001, then you can conduct the gap analysis internally.
- External Consultant: You can hire an ISO 9001 consultant for the gap analysis, which can help you objectively identify gaps for improvement.
Step 3 | Improve or Develop Your Quality Management System
Based on the gap analysis results, start developing or improving your QMS to meet the ISO 9001 standards.
- Document Your Processes: ISO 9001 emphasizes documentation, so ensure all critical processes, quality procedures, Quality Manual and Quality Policies are properly documented and available at respective areas.
- Define Organization Structure, Roles and Responsibilities: Make the organization structure and define Roles and Responsibilities so that everyone in the organization knows their roles and responsibilities clearly for maintaining quality system.
- Set KPIs/Quality Objectives: Establish quality objectives that align with the company’s Policy.
- Make a Continual Improvement Plan: ISO 9001 quality management system requires continual ongoing improvements, So create a mechanisms for reviewing and improving the established processes/systems. For example- Management Review Meeting (MRM), Internal Quality Audits like System Audit, Product and Process audits, Improvement activities like Quality Circles and Kaizen/Suggestions etc.
Documents for ISO 9001 certification
ISO 9001 Documents
Documents provide guidelines on how tasks should be performed. The main documents required for ISO 9001 QMS certification are:
- Quality Policy
- Quality Objectives
- Quality Manual
- Quality Procedures
- Organization Structure
- Process Interaction Map
- Contingency Plan
- Work standards or SOPs
- Process Flow Chart-PFC or PFD
- Failure Mode Effect Analysis-FMEA
- Control Plan
- Quality Inspection Standards
- Work Instructions
- Role and Responsibilities
- Approved Supplier List
ISO 9001 Records
Records provide proof that tasks have been performed as per the guidelines. Some common records of ISO 9001 QMS are:
- Quality Inspection and Test Reports
- Training Records- Training Attendance, Feedback and Effectiveness
- Management Review Meeting Records
- Internal Audit Records- System Audits, Product and Process Audits
- External Audit Records- Previous audit findings closure and effective status
- Production Records
- Customer Complaints Summary Register
- Internal Rejection and Analysis Reports with Corrective Actions
- Customer Rejection and Analysis Reports with Corrective Actions
- Supplier Audit Reports with Corrective Actions
- Supplier Performance Monitoring Records
- Internal and External Corrective Action Reports
- Machine Maintenance Reports
- Machine Maintenance History Cards
- Tools/Dies Inspection Reports
- Tools/Dies History Card
- Calibration Inspection Reports of Measuring Instruments and Gauges
- Calibration History Cards of Measuring Instruments and Gauges
ISO 9001 Formats
ISO 9001 Formats refer to the standardized templates or layouts used for different documents and Records. Some common Formats of ISO 9001 QMS include:
- Quality Inspection Check Sheets
- Quality Inspection Plans
- Internal Audit Plan and Schedule
- MRM Minutes of Meeting
- Maintenance Check Sheets
- Machine Maintenance Plans
- Daily Production Monitoring
- Tool/Die Inspection Format
- Purchase Requisition
- Purchase Order
- Material Issue Slip
- Training Plan/Calender
- Training Attendance and Feedback
- Training Effectiveness sheet
- Minutes of meeting format
- Check Sheets
- Tool/Die Development Sheet
Step 4 | Employee Training and Awareness
Employees play a major role in the effective implementation of your ISO 9001 QMS, So it’s very important to provide them with awareness training on ISO 9001 requirements and its benefits.
- Employee Training: Provide training on ISO 9001 QMS requirements and processes, QMS documentation, and any new role and responsibilities.
- Internal Qualified Auditors Training: Provide training to a few employees on “ISO 9001 Internal Qualified Auditors” to perform internal system audits, which are required to maintain ISO 9001 certification.
Step 5 | Conduct Internal Audits
Internal System Audits are a very important step in the ISO 9001 certification process. System audits help you verify that your ISO 9001 QMS is functioning effectively and meeting ISO requirements.
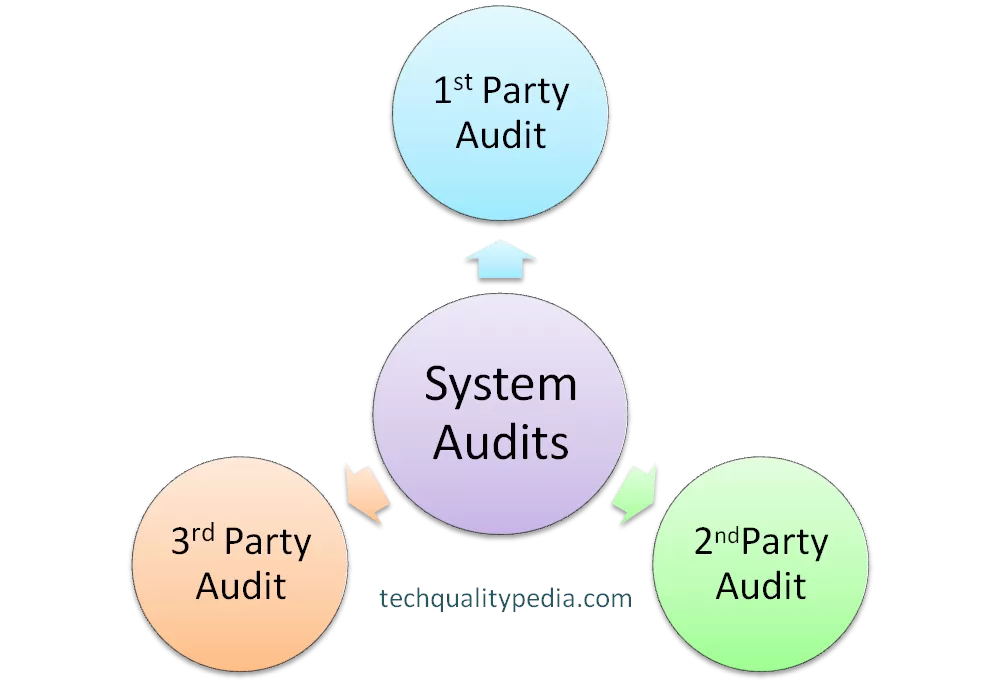
- Internal Audit Plan and Perform Audits: Prepare an Internal Audit Plan and Schedule to perform regular audits of your QMS processes to ensure compliance. The audit scope should include reviewing procedures, documents and records, observing processes, and interviewing staff/workers. Audit Check sheet must be available for the process/functions/department to be audited.
- Corrective Actions on Non-Conformities: If any non-conformities are observed during the audit process, corrective actions must be implemented to address the issues. The effectiveness monitoring of corrective actions must be ensured.
Step 6 | Select a Certification Body
A certification body is an external third-party organization accredited to issue ISO 9001 QMS certification. Selecting the best one is essential to ensuring your certification is recognized and respected. Some of the recognized certification bodies are: BSI, DNV, TUV SUD, TUV NORD, TUV Rheinland, ASR, SGS, DQS, Bureau Veritas, etc.
- Accredited Certification Bodies: Choose a certification body that is accredited by a national accreditation body, such as UKAS, ANAB, or DAkkS etc.
- Request Quotes: Get ISO Certification Cost estimates from multiple certification bodies to compare services and fees. Finalize the certification body based on budget and quality services offered.
- Schedule Certification Audit: Once you select a certification body, schedule your certification audit.
Step 7 | Certification Audit
The certification audit is performed by the certification body and is divided into two stages:
- Stage 1 Audit
- Stage 2 Audit
Stage 1 Audit | Documentation Review
The auditors will review your QMS documentation to ensure that it aligns with ISO 9001 QMS standards. This includes reviewing your Quality Policy, Quality Manual, Quality Procedures and processes, Management Review Meeting(MRM) plan and minutes records, and Internal Audit related documentation.
- Purpose: The aim is to confirm that your organization is ready for the final Stage 2 audit.
- Outcome: If any gaps are identified, you will have time to correct them before Stage 2.
Stage 2 Audit | Certification Audit
This is a more in-depth audit where auditors will evaluate your processes and procedures on-site. They will observe how your company operates, interview staff and workers, and review documents and records to ensure compliance with ISO 9001 standards.
- Outcome: If your QMS complies with the standard, you will receive ISO 9001 certification. If there are minor non-conformities, then you will need to correct these before the certificate is granted.
Step 8 | Receive ISO 9001 Certification
After the successful audit, the certification body will issue ISO 9001 certificate to your organization. This certificate is valid for three years, but during this period, you must maintain compliance with ISO 9001 QMS standards.
- Display Your Certification: Once your organization is certified, you can use the ISO 9001 logo and certification for your marketing and communications purposes.
- Certification Validity: Your certification is valid for three years but requires regular surveillance audits (at least once a year) to maintain it.
Step 9: Surveillance Audits
To maintain your certification, the certification body will perform regular surveillance audits (Once or twice a year). These surveillance audits are less comprehensive than the initial certification audit but are still very critical for ensuring continuous QMS compliance.
- Prepare for Surveillance Audits: Ensure to update all documents and records, continue to perform internal audits and management reviews, and address any non-conformities before the surveillance audit.
- Ongoing Improvement: Take necessary corrective measures against the surveillance audits to continuously improve your QMS.
Step 10 | Re-certification
At the end of the three-year certification cycle, you will need to undergo a Re-certification Audit to maintain your ISO 9001 certification.
- Re-certification Process: The Re-certification audit is similar to the Initial Certification Audit and is necessary to ensure continued compliance with the ISO 9001 QMS standard.
Conclusion: Achieving ISO 9001 Certification
ISO 9001 QMS certification is an investment in your organization’s future, improving effectiveness and efficiency, and enhancing customer satisfaction and competitiveness. By following the above steps — understanding the requirements, developing your QMS, conducting internal system audits, and choosing the right certification body, you can successfully obtain ISO 9001 certification and reap its many advantages