There are mainly two types of major changes occurred in manufacturing processes/industries.
- Permanent Change – For Example ECN/PCN Change
- Temporary Change – For Example 4M Change
Table of Contents
4M CHANGE TYPES
4M Change types are:
- MAN CHANGE
- MACHINE/TOOL CHANGE
- METHOD CHANGE
- MATERIAL CHANGE
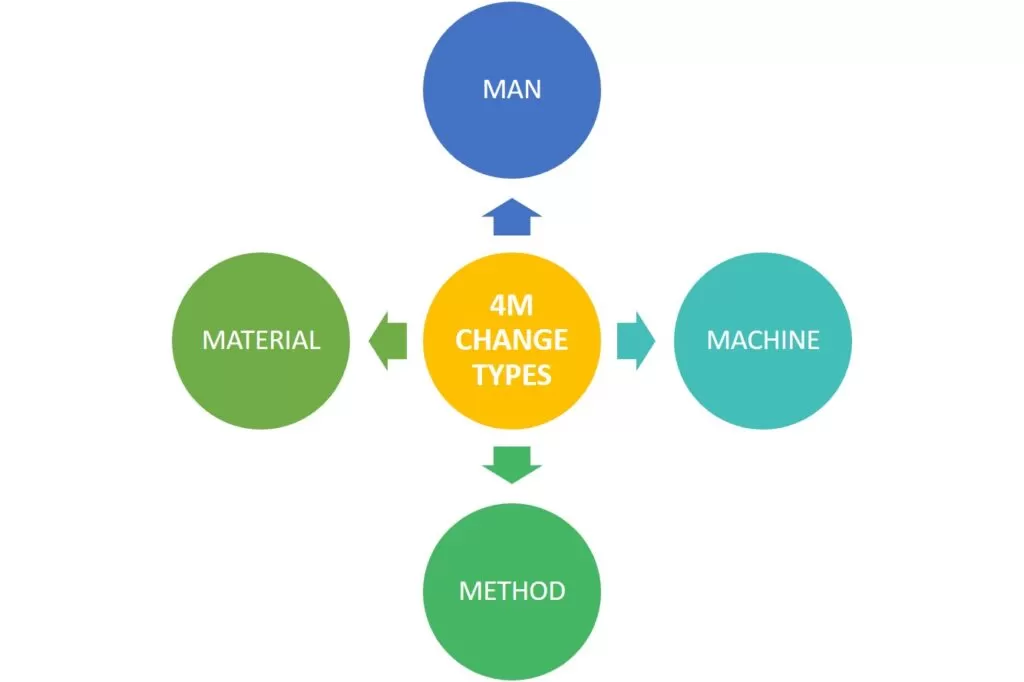
CHANGE RELATED TO “MAN”
- Skill level change
- New Operator
- Extra & Extended shift working
- Contract manpower
- Operator dominant process operator change
- Skill level change (Inspection & Critical Station)
CHANGE RELATED TO “MACHINE”
- Tool & Die change (new / duplication)
- Machine change i.e. Change in Type, Capacity etc.
- Production done after Tooling In-Active
- Change in Die & Tool -core, cavity, insert, slider etc. (change in part feature)
- Ejector pins, nipples & part non-feature segment change in tool.
- Cavity, Jigs, Fixtures, tool segment increase
- Cavity, Jigs, Fixtures, tool segment decrease
- Change in Tray, Jig & Fixture
- Soldering and conformal coating fixtures change
- ICT & FCT fixtures / software change
- Welding fixtures change
- Removal / Addition of Poka-yoke
- M/c parameter change & Process Parameter Change
- Tool & Machine Accident
- Power Source Changed
- Machine internal change for same capacity
CHANGE RELATED TO “METHOD”
- Process sequence change
- Any temp deviation from Control Plan/PQCS
- New Technology
- Sub-process supplier change
- Process Deletion, Merging, Elimination, Additional
- Bin/Trolley (WIP/Storage/Dispatch)
- Packaging change
- Traceability (Batch Code) marking Change
- Limit Sample Change
- Transportation mode change
- Number of material handling
- Traceability (Batch code) marking change
- Inspection marking change
- Inspection method, Frequency & Equipment
CHANGE RELATED TO “METERIAL”
- Raw material size / thickness / weight change
- Different raw material approved supplier
- Different spec / grade
- Different raw material unapproved supplier
- Change in Consumables i.e. Oil, Grease, Flux , Solder Paste, etc.
- Child-part change (Machine)
- Child-part change(Method)
- Child-part change (Supplier)
- Child-part change (Material)
ENGINEERING CHANGES
- Customer requested engineering changes
- Internal Change request affecting customer fit / function
- Internal Change request affecting customer Appearance
- Internal Change request affecting product life cycle
- Internal Change request not affecting customer Fit/Function/Appearance/Life cycle – For facilitating Rejection reduction, Poka-Yoke, Ease of inspection, productivity improvement, and Assembly process.
MANUFACTURING LOCATION CHANGE
- Tool Transfer Inhouse
- Process Transfer to other location (Inhouse)
- New location / layout change
- Work station change
- Re-located after 6 months
- Change can affect the legal requirements and Environment
REASONS FOR CHANGES
- Customer requirements
- Warranty complaints
- In-house complaints
- Productivity improvement
- New or Modified Tools, Dies, Molds. etc.
- Die/Tool transferred
- Refurbishment or Rearrangement of existing tooling or equipment
- Change in test / inspection method
- Change in process flow / method that impact fit, function, form performance and durability
- Identical gauge replacement.
- Assembly line shifted from one plant to another.
- Missing cavity in regular production
- Product produced after the tooling has been inactive for volume production for 12 months or more
DOCUMENTS SUBMISSION AGAINST 4M CHANGE
Following document are generally submitted to customer (as per requirement & applicability) against the 4M Change or any Engineering Change:
- Setup approval report
- Material/part Inspection report
- Part Submission Warrant
- Material/Performance Test Results
- Appearance Approval Report (AAR)
- Master Sample – To be identified and retained by the supplier
- Process Flow Diagram
- Measurement System Analysis studies (MSA)- e.g. Gage R&R for all measuring instruments used in part inspection as per control plan. Sample Inspection (Dimensional) Report
- Calibration Plan
- Preventive Maintenance Plan
- Control Plan/PQCS/Work Standard
- Process Failure Mode and Effects Analysis (PFMEA)
- Records of Compliance to Customer-Specific Requirements
- Qualified Laboratory Documentation