Manufacturing Process Audit Check Sheet points requirement as per IATF 16949 clause no. 9.2.2.3 are:
- The relevant documents like PFC, process risk analysis (such asPFMEA), control plan, SOPs, and associated documents must be referred for effective manufacturing process audit.
- Audit all manufacturing processes over each three-year calendar period.
- Audit of all shifts for effective control on process and product quality i.e. process audit must cover all shifts e.g. day and night shifts both.
- Using customer-specific required approaches else determine the approach to be used i.e. all the customer specific requirements must be included in the process audit.
The Manufacturing Process Audit Check Sheet points related to Man, Machine, Method & Material requirement are described below:
Table of Contents
MAN Related Check Points
(Observe Machine Operator)
- Is operator trained & competent to operate equipment being audited?
- Is Operator deployed as per their Skill matrix?
- Is the control plan being followed by the operator?
- Audit the operator performing control plan checks (product audit).
- Is the operator familiar with the Reaction to Abnormal Conditions?
- Does operator know the customer and application that uses the parts? (If no, advise the operator.)
- Is the operator properly identifying product and segregating good material from bad material?
MACHINE/EQUIPMENT Related Check Point
(Observe Machine/Equipment/Tool/Jig/Fixture)
- Check Machine / Equipment Condition (Appearance, Noise, Vibrations etc.).
- Are the inspection items, inspection frequency and criteria for each equipment clearly defined and do you perform the daily inspection and periodical inspection?
- Do you standardize the cutting tool change time, grind stone redressing time, and electrode dressing frequency and perform them exactly?
- Is the procedure to check/ correct the possible defectives that have been produced, when a problem happens in production equipment/ tools/ jigs, defined?
- Do you make Maintenance check sheet and record the periodical inspection , maintenance and repair history, Calibration?
- Are the check result recorded on the check sheet/ history sheet etc.?
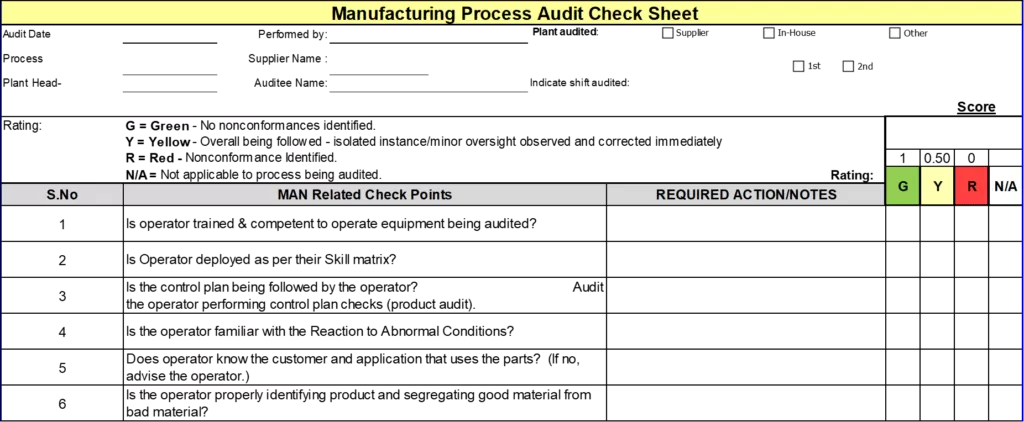
MATERIAL Related Check Points
(Observe – Material Flow/Condition)
- Do you specify the part number , quantity, manufacturing date etc. on the material, stocks, extra product& spare parts etc.
- Do you have old products in the stocks.
- Do you ensure first-in-first-out precisely with the parts tag or lot display etc.
- Do you take any action to prevent the dust, rust, crack, moisture & rain etc. for stocks & unfinished products.
- Are the packing style & storage environment controlled with consideration to contamination.
- Does the packing method prevent transportation damage.
METHOD Related Check Points
(Observe Method)
- Is the operation carried out according to the standard? ( Is the check method for ensuring the implementation of operation standard clear)?
- Is the quality check for observance of operation standard carried out as decided?
- Is the check result recorded on the check sheet etc.?
- Is the section & person for preparation of operation standards and the approval agency etc. are defined in the procedure?
- Do you display/ keep it at the convenient location to see and pick up as required?
- Are the quality check items, frequency ,criteria and measurement method specified?
- Is the procedure for revision & revision history clear and is it carried out according to the procedure?
- Do you control the revision of related standards based on the changes to drawings?
- Is the reason for non-conformance specified in the non-conforming products.
- Do you analyze the defect causes and carry out defect reduction activities continuously company wide.
- Do you display the calibration due date on the measuring equipment & use it within the due date ?
- Are there any boundary/ limit samples to judge objectively for visual inspection?